Since the production of telepresence robots was relocated to France at the end of 2020, Awabot has been striving to apply eco-responsible practices in the manufacturing process of Beam® telepresence robots. This is a major challenge in the field of robotics, where many electronic components and other raw materials come from the other side of the world, especially Asia. But Awabot has not yet said its last word.
Beam®: A Robot Designed to Last
First of all, two key elements make Awabot a company with a fundamentally more sustainable production method: the robustness and reparability of its products. Ensuring the durability of our solutions depends above all on guaranteeing their quality. This is why the Beam® telepresence robot is designed to last thanks to materials and parts selected for their sturdiness. If hardware optimizations come into play, they go hand in hand with software improvements.
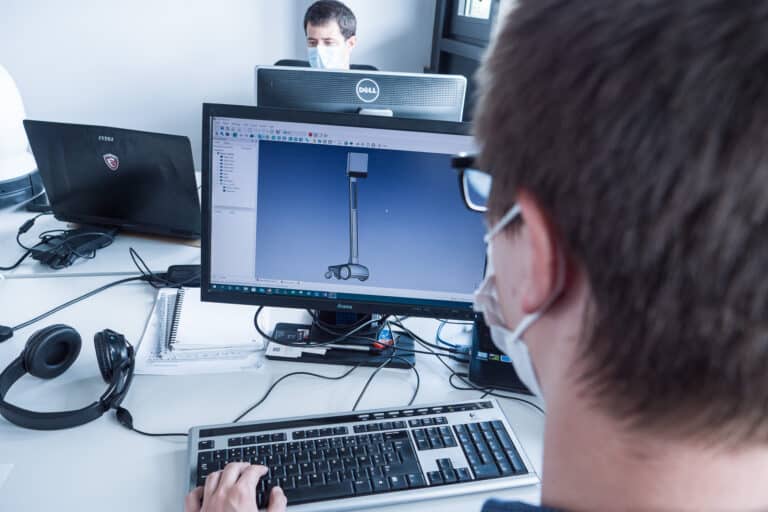
Indeed, software updates also allow us to maximize the longevity of our machines. Moreover, our products can be completely dismantled, from A to Z, from the base of the robot to its head. Each element of the device can be repaired in our workshop, or be recovered for the maintenance of another device. As far as possible, nothing is thrown away, everything can be repaired.
Nothing is Lost, Everything is Transformed
Some parts that have reached the end of their life, after having allowed long hours of exchanges in telepresence, cannot be reused. This is the case of the batteries in particular. But throwing them away is out of the question! They are recovered by a third party so that the acid they contain can be removed, and the lead and plastic they contain can be recycled in an appropriate manner.
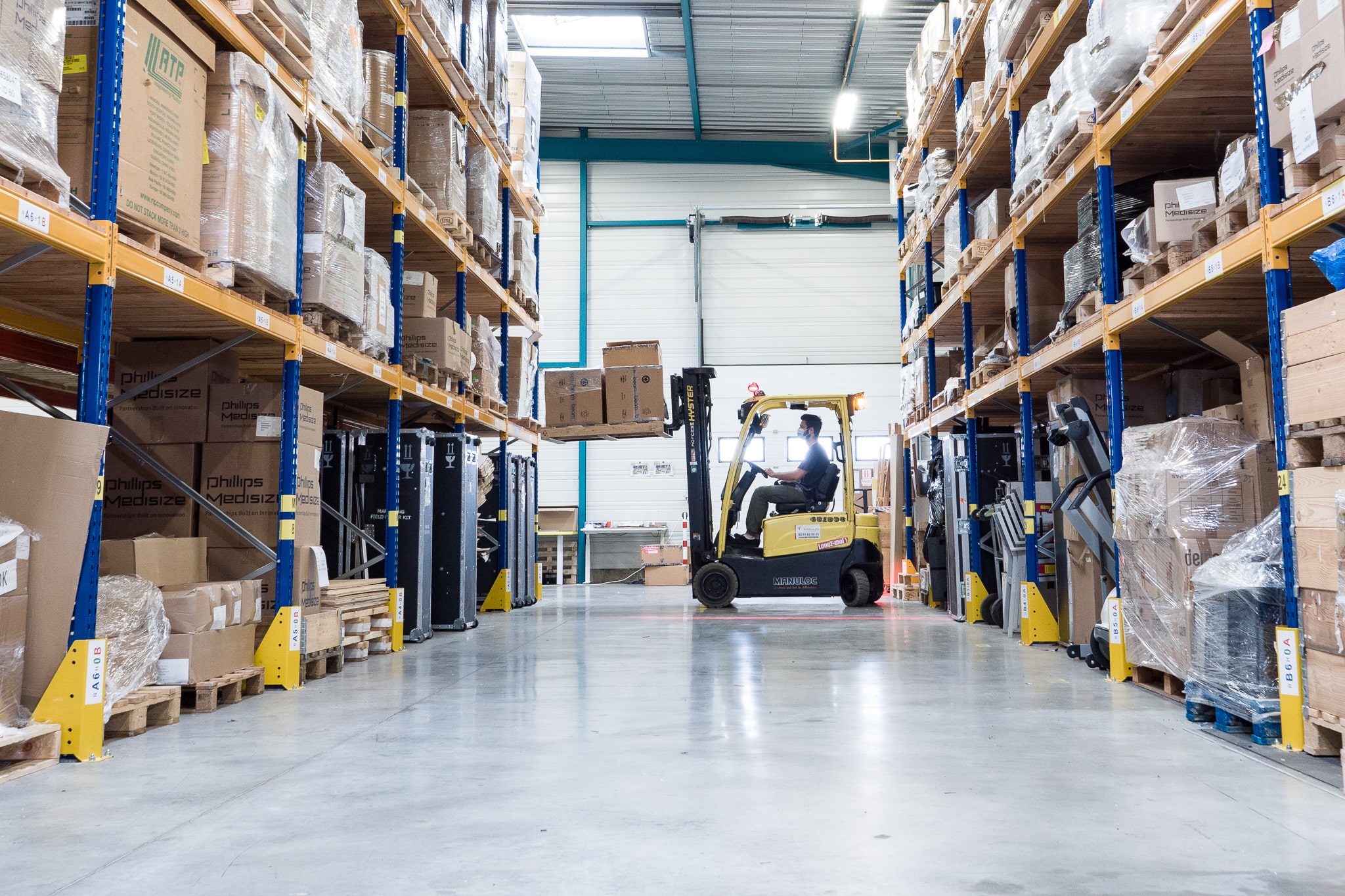
If batteries are recycled, the same goes for plastic or electronic components, as well as paper or cardboard, which certainly do not end up in the dumpster, but in recycling bins. These are good practices to minimize waste, and employees in the production chain are regularly made aware of them. Thanks to these measures, waste from robot production rarely exceeds 5% of parts. A circular economy model is thus applied within our production chain.
Combining Profitability and Eco-Responsibility
Achieving an economically viable and ecologically ethical production mode is not an easy task for a telepresence robotics manufacturer. Therefore, Awabot tries to subcontract as little as possible not only in order to respect the environment, but also to ensure the quality of our products. When we do use intermediaries, we prefer to work with local suppliers as much as possible.
For example,
- The plastic of which the Beam® telepresence robot is made is injected locally in the Auvergne-Rhône-Alpes region.
- The transport box of the device is made of a monomaterial for easier recycling. It is currently manufactured in Barcelona but the objective is to achieve a production closer to the Lyon metropolis, where our company is located.
- The painting of the robot, the realization of the fasceaux, the insertion of the plastic parts, or the supply of all “custom” electronic cards are outsourced via local service providers.
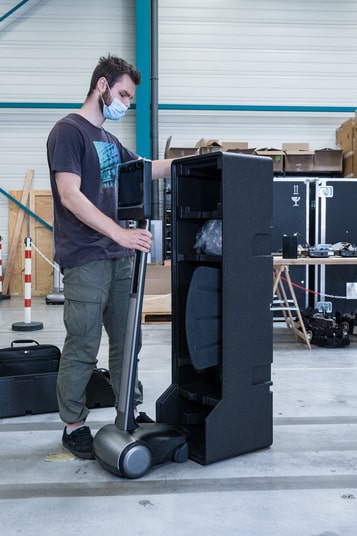
Unfortunately, logistical and economic realities make it sometimes not viable to be supplied locally. This is particularly true for electronic components, where the majority of providers are located in Asia. The objective is therefore to adopt a rational consumption of spare parts by avoiding waste at all costs and by reusing any part that can be reused.
A Production Rate on a Human Scale
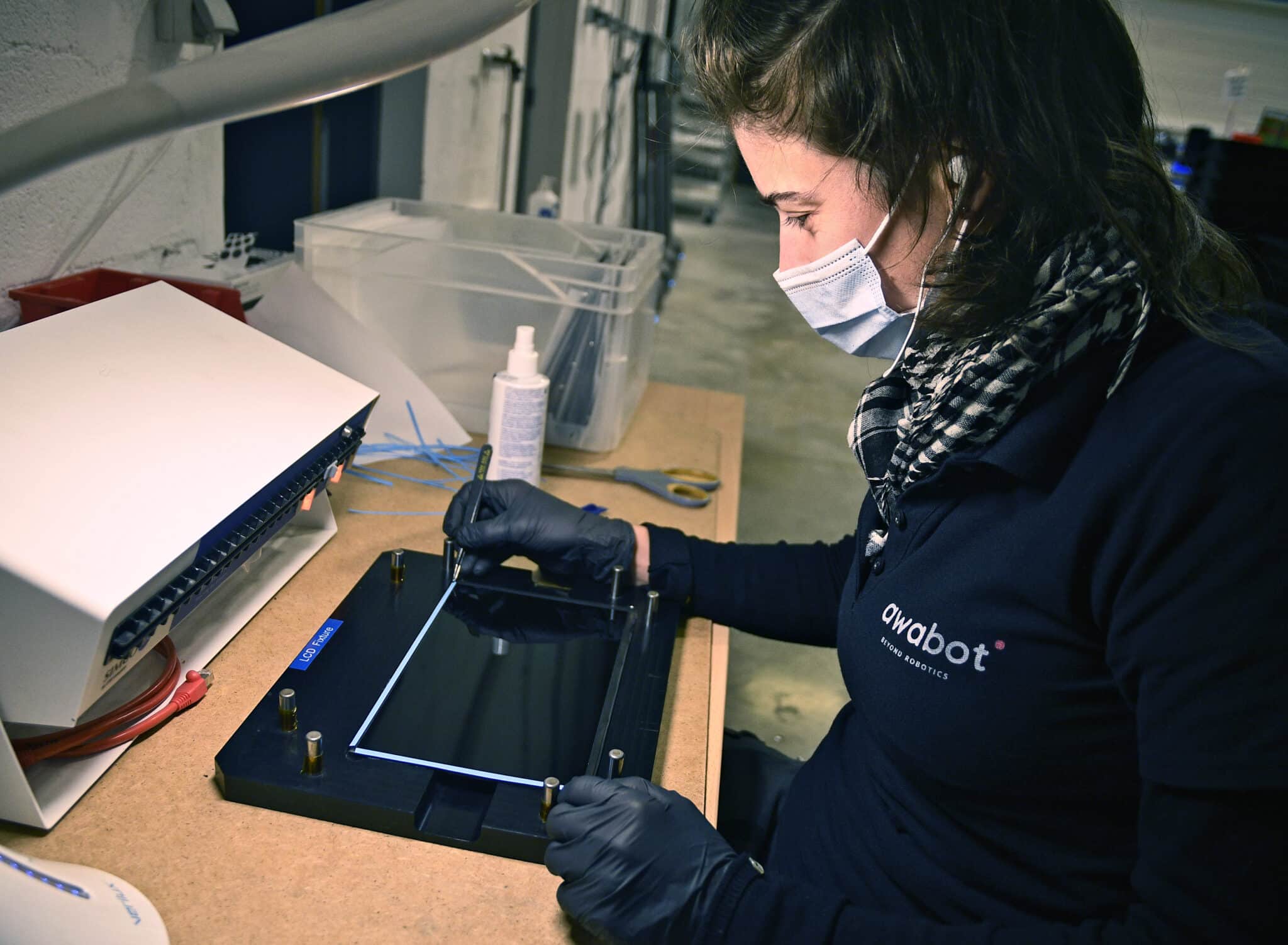
Building telepresence robots is not something you can improvise. On the contrary, robotics is a field where precision is required. Each component must be handled with care. The employees working on the production lines are thus confronted with high requirements in order to ensure the quality of the finished product. However, there is no question of manufacturing at a frantic pace. Our daily production targets are set in such a way that they are both economically and humanely viable.
Indeed, if the control of deadlines and costs are major production objectives, the quality of our solutions and the safety of our employees are paramount. Ensuring the safety of our employees involves, first and foremost, wearing personal protective equipment (gloves, glasses, shoes). In addition, all chemicals that could be hazardous to humans and the environment, which could previously be used in the manufacturing process, have been banned and replaced with safer alternatives.
Well-being in the workplace is also one of our main concerns at Awabot. This is why we have sought to put in place initiatives to establish a more participative management. At the workshop, this is illustrated by the creation of a suggestion box in which employees can share their production-related ideas. This initiative is already bearing fruit, particularly in terms of the comfort of workstations, where the seats have been replaced to improve ergonomics.