Automation is growing by leaps and bounds in warehouses. Operators now see AMRs and other AGVs circulating in the aisles. Supply chain logistics is constantly evolving, and professionals are facing multiple challenges combining productivity, economic profitability and ecological and social impact. But how do automated logistics and mobile robotics respond to the supply chain issues? This was the subject of a round table discussion held during the last edition of SIDO in Lyon and which brought together Damien LEGRAND – Head of 3D Perception & Logistics Market – IFM, Alexandre AMBIEHL – Director of R&D programs – E-COBOT, and also, Florian CANTORI, Lead Robotics Software Engineer – AWABOT INTELLIGENCE.
AMR / AGV: what are the differences?
Autonomous Mobile Robots (AMR) and Automated Guided Vehicles (AGV) can both relieve operators of the burden of transporting heavy loads and automate logistics flows. Their difference lies in the degree of autonomy of these solutions:
- the mobile robot will move freely in the environment according to a map built with SLAM or visual SLAM algorithms;
- the “Automatically Guided Vehicle” will only move if it follows a predetermined path materialized by rails or markers on the ground.
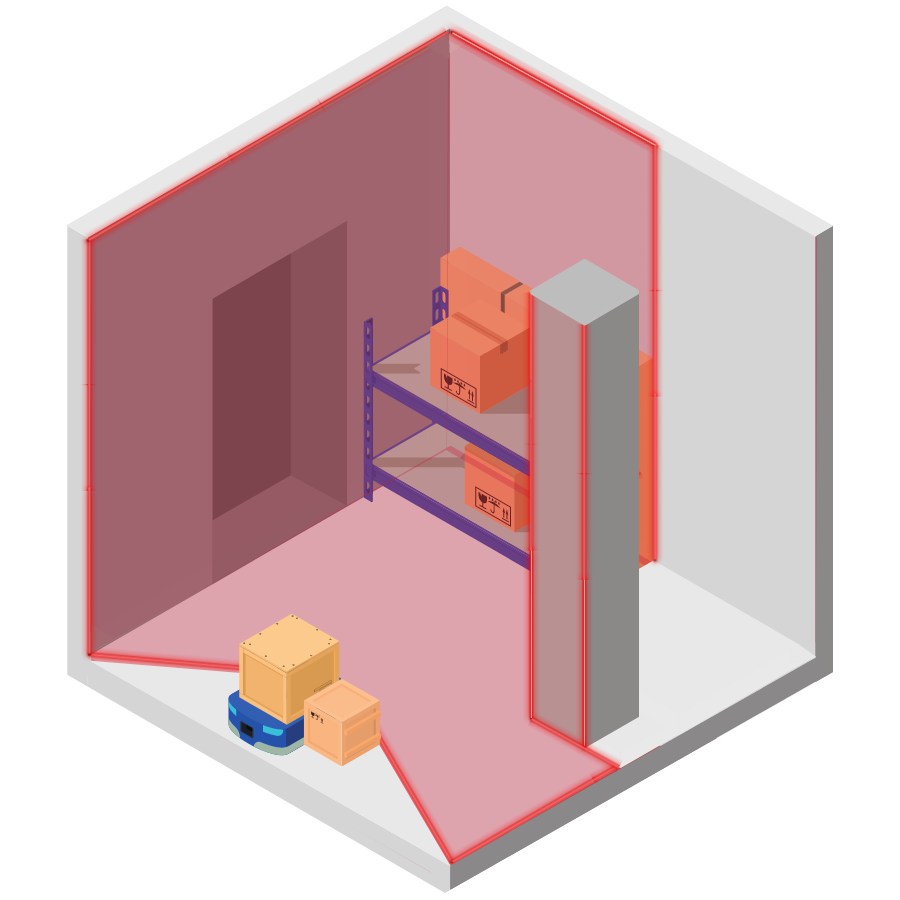
Autonomous Mobile Robots (AMR)

Automatically Guided Vehicle (AGV)
Mobile industrial robots to reduce work life drudgery
Both systems are used to perform low value-added tasks, such as carrying heavy loads over several meters. The operator can then concentrate on other more complex tasks or those subject to variability (e.g. handling elements of multiple shapes or sizes). Indeed, automation is only relevant for standard and repetitive tasks. Mobile industrial robotics solutions are also popular to reduce the drudgery of certain operations. Automation and robotization of processes are particularly well suited to the risks associated with difficult or even dangerous working conditions.
Supply chain: tailor-made mobile robotics solutions
There are no “standard” robots for industry: each solution is established according to the customer’s needs and its logistical and industrial environment.
“In terms of software, the business context is the driving force of the robotics project from the very beginning of the design stage. Mobility is not everything. Understanding the final use case and its stakes for the customer is essential in order to maximize the use of the AMR. It must integrate as naturally as possible into the environment it is designed for, alongside the humans around it,” explained Florian Cantori, expert in software solutions for robotics.
Interactions with the environment are therefore essential: it should preferably be stable and orderly. Indeed, the mission and availability rates are very dependent on the spaces according to how clean they are, the state of the items to be transported, or the obstacles that can deviate the trajectory taken by the robot.
Thus, each solution based on mobile robotics is unique as it takes into account the business need, the logistics site and its surface area, and of course the customer’s budget.
You want to discuss a project related to the topic discussed in this article? The Awabot Intelligence team has the know-how and complementary skills to cover all the issues related to robotics. Contact us now!